Expert
Carpet Installation
Get a flawless carpet installation with our professional services at Floor Craft.
Request an Estimate Today
You'll discover a unique difference when you
shop at Floor Craft in Colorado Springs, CO.
Experience the Difference
Seamless Carpet Installation in Colorado Springs, CO
Before and During Your Installation:
Here is what you can expect before your carpet installation with Floor Craft:
- We will walk you through the entire installation process before we begin. This is a good time to ask any questions that you might have.
- Please ensure that children and pets are not present during installation day.
- Complete any painting that might need to be done before we begin the installation.
- Ensure that someone 18 or older will be present on installation day.
- Remove any furniture or fragile items from the room in question.
- Be prepared not to have access to the rooms where the installation is set to take place.
During Your Installation:
Expect the following during our carpet installation process:
- Your existing flooring may need to be removed, and your subflooring may need to be prepared.
- Your team may need to remove doors, depending on the room(s) in question.
- The underpad will be laid.
- The crew will match up the carpet seams.
- The carpet will be stretched and attached to the floor.
- We will do our clean-up and quality control check.
After Your Installation:
After your carpet installation, the following should take place:
- We will walk you through the installation and allow you to ask any questions that you might have.
- Run a fan to remove any installation-related smells.
- Allow your floors and the materials to settle before walking across your carpet. At least 24 hours should pass before you use the carpet.
- Stay in touch with our team with any questions about your new carpet.
More about carpet
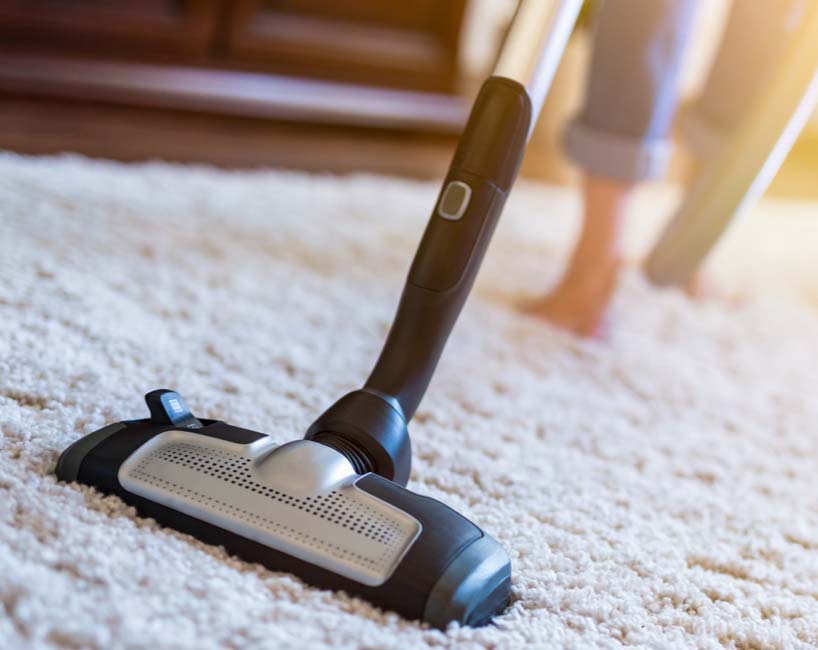
Carpet Care
Learn how to keep your floors looking their best.
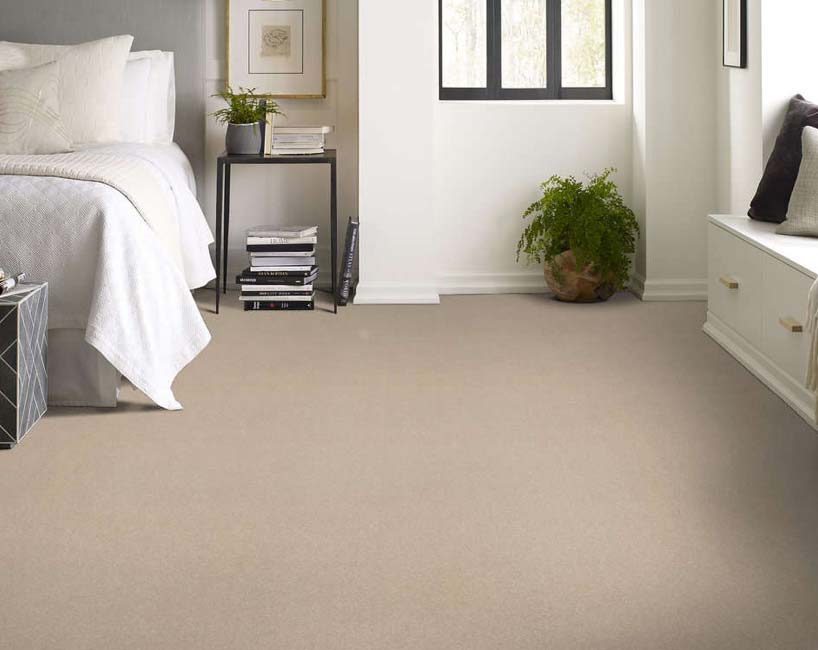
About Carpet
Carpet is a great choice for many homes.